商品の色ってとっても大事! ~精算機用取付けパネルの塗装色誤りが引き起こした問題とその教訓~
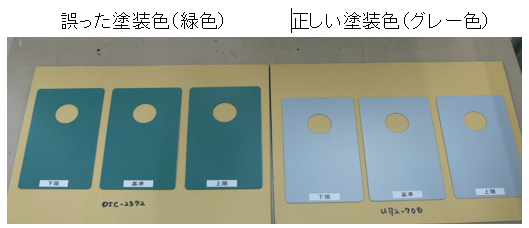
生産本部 調達部の沢本です。
今回は精算機用の取付けパネルの塗装色間違いのお話です。
商品の色って、お客様にとっては非常に大事な要求項目だと思っています!
内容としては少々レベルの低い話ですが、発生原因をググッと掘り下げてみたいと思います。
受入検査の基本
- ①あたり前のことですが、まずは仕様(お客様がどう言った商品を要求しているか?)の確認をおこないます。
*仕様と言っても、寸法、材質そして塗装色、物によっては機能の確認も必要となります。
- ②次に現物と仕様書との確認
*特に塗装色については、単なる色だけではなくて表面の仕上げの状態など(表面処理の有無や色艶など)確認が難しいものは色見本を取り交わして比較確認します。
今回の不具合は、上記の②はおこなったのですが、大事な①が出来ていなかったというお話です。
原因の整理
では、なぜこんなあたり前のことが抜けたのか?
作業者と私(指示者)の各々の立場での行動、行動の理由、反省点を整理してみました。
また、受入検査をおこなうにあたって、社内のルールやその運用がどの様になっているかを改めて確認してみました。
(前述の①,②がルール化されているかの確認)
- (a)作業者が実施するためのルールは下記の通り整備されており、受入検査の確認方法も理解していたが、実際の作業時に守られていなかった。
・「発注内容との一致確認」
・「塗装仕様書NO.(内容)との一致確認」
・「色見本との一致確認(色型式確認)」
(b)(a)のルールが実際に徹底される運用(第三者による確認手段等)は無かった。
指示者(私)は、当然ルール通りに実施するものと思い込んでいた。
*作業者が確認作業を行うためのルールは有ったが、守らなかった。
*ルールが実際に徹底される運用は無く、確認がされなかった。
上記の2点が重なったため、不具合を発生させてしいました。
根本原因
・原因1・・・馴れと思い込み
⇒不具合原因の根本を突き詰めていくと、殆どは馴れとか思い込みによる人為的なミスに行き着くものだと改めて知らされた。
・原因2・・・ルールを徹底するための確認方法
⇒基本ルールを守られているか?の確認行為の大切さを痛感した。
対策内容
調達部として受入検査確認リスト表の確認内容に沿って再教育を行い、以下の運用を行うこととしました。
・作業者は、受入検査確認リスト表に沿って作業を実施し確認記録を必ず残す。
・指示者(私)は、確認記録に記載されていることの確認を行う。
また社内品質朝礼での発表を通じて、受入検査の検証内容を社内にも共有致しました。
現在では、半年間の経過観察により作業者に任せられるレベルと判断し、指示者による確認作業を無くしましたが同様の不具合は発生しておりません。
まとめ
幸いにも今回は、製品出荷前に製造部より色の違いを指摘頂いたため、社外への流出はありませんでしたが、自分達のミスは絶対次工程に送らない(次工程はお客様)と言う意識が必要であると認識しました。
「この場を借りて、製造部の皆さん、ありがとうございました。」
今回の事象より、作業者が実施するルールの問題だけではなく、決められた検査確認方法が実際に徹底されているかを確認するルール作りが重要であることを再認識しました。
「当たり前のことを何よりもちゃんとする。」の社風通りの行動が実施出来る仕組みづくりを心掛けます。