どこに消えた?1円硬貨!? こんなところに隙間が・・・!!
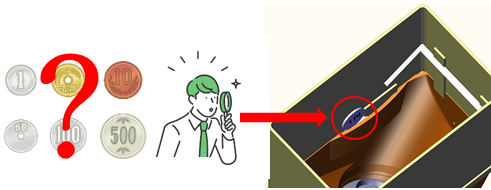
それでは参ります。
今回掲載する製品は、これまでも度々登場している外貨両替機(AES-ME1.5)。
その名の通り簡単に説明すれば、外貨を日本円に両替してくれる機械。
インバウンド旅行者(観光やビジネス、留学などの様々な目的で日本を訪れる人)をターゲットとした便利な製品です。
最近では海外向けとしても出荷がチラホラ。
現在の為替レートの確認とかもできちゃうんで見かけたら気軽に触ってみてください。
“関連製品資料”↓
https://arunas.co.jp/product/aes-kme.html?hsCtaAttrib=150590860046
★「硬貨回収時に1円足りない・・・」
問題が発生したのは、某大型ショッピングモール内に設置された外貨両替機。
設置して1週間後、回収員がお金の回収を行なったところ、問題が発生。
製品が払い出したと言っている金額(枚数)と実際に払い出された金額が合っていない!
・・・1円が足りていない!ゾ
回収員による不足硬貨の捜索開始。
(速やかに回収作業を行なう必要があるところ、時間とらせて申し訳ない)
~捜索時間およそ1時間・・・・・・。
★「発見!・・・こんなところに挟まっている?」
回収員により払い出しされなかった1円硬貨発見!
これは外貨両替機内に搭載されている1円硬貨が収納されているホッパーというデバイスの内部。
この中に硬貨が収納されていて、上位側からの指示でモーターが働き、硬貨が払い出されます。
こんなところ(なぜ隙間?)に挟まって、詰まって、払い出しがされない状況でした。
ホッパー(払い出すデバイス)も可哀想に、、、
上位側が出せと指示しているのに、払い出そうとしても出せないという事態。
もがいてモーターまで焼き付かなくてよかった。
★「隙間の原因を掘り下げ~探れ」
回収員が挟まっていた箇所も見つけてくれたので、原因追及はそれ程難しくありません。
ここでホッパーの構造をご説明。
外貨両替機に搭載している硬貨ホッパーは、ホッパー本体の硬貨収容部(ホッパーヘッド)にメーカオプションの増量ヘッドを取り付けた構成。<図1>
このホッパーが外貨両替機1台に3金種(100円、10円、1円)が搭載されており、この3金種混合にて硬貨の両替金払い出しが行なわれます。
ホッパーヘッドの上部エッジ部に増量ヘッドの嵌め込みガイド(爪)が嵌まり込んで、取り付けられています。<図2>
正規に一回嵌め込めば、簡単には取り外すことはできません。
今回発生した障害は、このホッパーヘッドへの増量ヘッド取り付けにおいて、嵌め込みガイドが正規の位置に嵌まり込んでおらず、1.5mm程度の隙間が発生。その隙間に1円硬貨が挟まったものでした。<図3、4>
あ~~、こんな初歩的な組立ミスをするなんて・・・
今まで出荷したものは大丈夫??でも不具合連絡来てないからなぁ・・・大丈夫かな!?
こういった心配が頭をよぎりました。
さて、そんな心配を抱えながらも硬貨の出金不良は掴めたところで、次は製品の不良となる波及性(単体?ロット?全数?)の調査開始。
因みに当時、この外貨両替機は出荷フィーバーを迎えていて、ほぼ毎月のようにロット生産(21台)を繰り返していました。
1台を完成(組立~検査~キッティング)するだけでもかなりの工数を要するマンモス製品。
1台20時間以上掛かってた覚えがあります。
当然一人ではこれらの台数を完成まで持って行くのは不可能で、部員の他、派遣社員様・協力企業様の力を借りて、日々製品生産に没頭している毎日でした。
(それはそれで楽しくて、人使いの荒い自分に向いていたけど)
余談はさておき、該当ロットについて出荷済台数は21台中4台。
このロットより、生産増大に向けて、該当ユニット部(硬貨ホッパーユニット)の組立を協力企業様へ展開。
言い換えれば、4M変更となる作業者と生産場所の変更が発生していたことになります。
作業者(協力企業様)へのヒアリングと生産展開に伴う、指導・引継ぎ状況などの変化点を調査。
ちなみに引き継ぎした犯人は僕ですけど・・・
以下原因
- 引き継ぎ資料(作業指示書)の注意点記載漏れ
- 1に伴い、作業者への注意点説明漏れによる作業者の理解不足
- ユニット受入検査時の確認項目漏れに伴う、チェック検出漏れ
調査の結果、組立不良が発生しているのは、該当ロットのみと特定できました。
総数21台(出荷済品4台・出荷待ち品2台・仕掛り品15台)に対しての全数確認と処置を実施。
金種は異なりますが、数台で発生。出荷している製品もまだ少なかったのが救いです。
これぐらいの組立、説明無くてもミスせずやってよって思いましたけどね。(すみません愚痴です)
しかしながら、この障害から得たものは大きかったと。
★「最後に・・・失敗を経て」
組立といっても様々で、ビスの締付や部品の取付け、デバイスの位置調整、ハーネス配線、シール貼り等々、人の得意・不得意の力量を把握して作業配置していく訳で、社内であれば目も行き届くので作業状況の監視や確認は取り易いです。
ですが協力企業様など場所が変わって目の行き届かないところですと、作業状況が見えないことで予想していないことが発生する場面もあります。
本件の失敗は、引き継ぎ資料(作業指示書)に記載が無く、指導する側としてもしっかり説明できていなかったこと、このようなミスが発生すると想定できていなかったところが真の原因であると反省。
自分の頭の中にあるノウハウであったり、情報をいかに伝えられるか、伝え漏れを起こさないかにかかってきます。
引き継ぎ漏れを起こさない為にも、しっかり資料に落とし込むことを念頭に作業指示書の重要性を痛感した事案です。
今では部員・派遣社員様の多くの作業者を管理していく立場でもあり、作業者の力量もそれぞれで、熟練者・初心者・素人、誰から見ても分かる資料への落とし込みが要求されます。
本障害以降、我が社の生産資料もどんどんとブラッシュアップされ、今では非常に良い資料に出来上がってきています。
お客様に満足頂ける製品を常にお届けできるよう、私達は日々品質向上を目指し、安定した生産の実践・実現に取り組みます。
では、また機会があれば